Thermoforming
Thermoforming
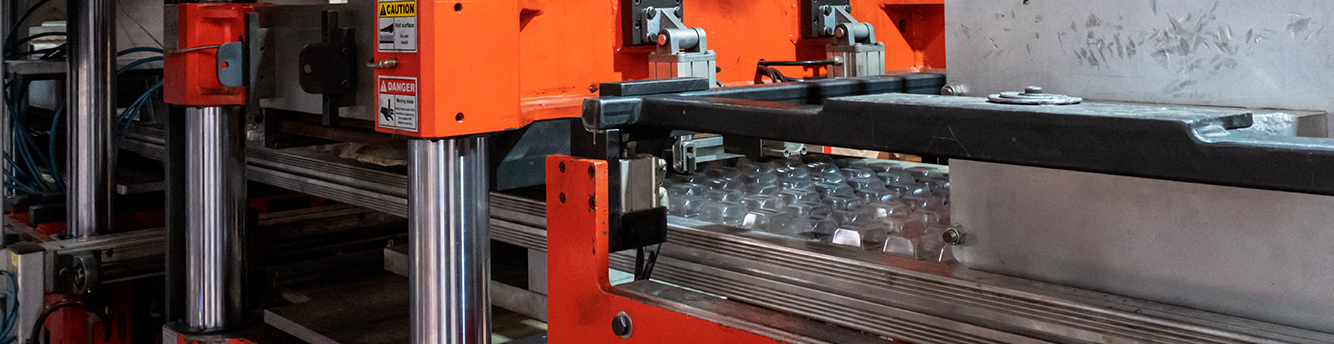
Thermoforming is a manufacturing process used to shape plastic sheets into specific forms by heating and molding. The process offers several advantages, including cost-effectiveness, versatility, and fast production times. It allows for the creation of complex shapes with high precision, using a wide range of materials. Thermoforming is ideal for producing both small and large quantities of parts.
Here’s how it works:
- Material preparation: A plastic sheet (typically PVC, polystyrene, or polyethylene) is placed onto a clamp frame.
- Heating: The sheet is heated in an oven until it reaches its softening point.
- Forming: Once heated, the soft plastic sheet is stretched over a mold or pressed into it using vacuum suction, air pressure, or mechanical force.
- Cooling: The plastic is held in place while it cools and solidifies, taking the shape of the mold.
- Trimming: The formed plastic is trimmed to remove excess material and achieve the desired final shape.
Common materials used in thermoforming include Acrylonitrile Butadiene Styrene (ABS), Polyethylene (PE), Polypropylene (PP), and Polyvinyl Chloride (PVC). These materials are selected for their specific properties like strength, flexibility, and transparency.
Examples of products and solutions we offer for various industries:
- Packaging: Blister packs, clamshell packaging, and food trays.
- Aerospace: Interior panels, seat backs, and overhead compartments.
- Medical: Disposable medical trays, packaging for sterile products, and diagnostic equipment housings.
- Automotive: Interior panels, door liners, and protective covers.
- Consumer Electronics: Housings for electronic devices and product casings.
- Retail Displays: Point-of-purchase displays and product trays.
- Food and Beverage: Disposable food packaging, cups, and lids.
- Household Appliances: Refrigerator liners and washing machine panels.
Examples of industries we serve:
- Automotive
- Agriculture
- Marine
- Industrial
- Playground and Recreational Equipment
- Construction
- Consumer Goods